క్రోమాటిక్ అబెర్రేషన్ అనేది ప్రింటింగ్ పరిశ్రమలో వంటి ఉత్పత్తులలో గమనించిన రంగులోని వ్యత్యాసాన్ని వివరించడానికి ఉపయోగించే పదం, ఇక్కడ ముద్రించిన ఉత్పత్తులు కస్టమర్ అందించిన ప్రామాణిక నమూనా నుండి రంగులో తేడా ఉండవచ్చు. పరిశ్రమ మరియు వాణిజ్య రంగంలో క్రోమాటిక్ అబెర్రేషన్ యొక్క ఖచ్చితమైన మూల్యాంకనం చాలా కీలకం. అయినప్పటికీ, కాంతి మూలం, వీక్షణ కోణం మరియు పరిశీలకుని పరిస్థితి వంటి వివిధ అంశాలు రంగు మూల్యాంకనాన్ని ప్రభావితం చేస్తాయి, ఫలితంగా రంగు వ్యత్యాసాలు ఏర్పడతాయి.
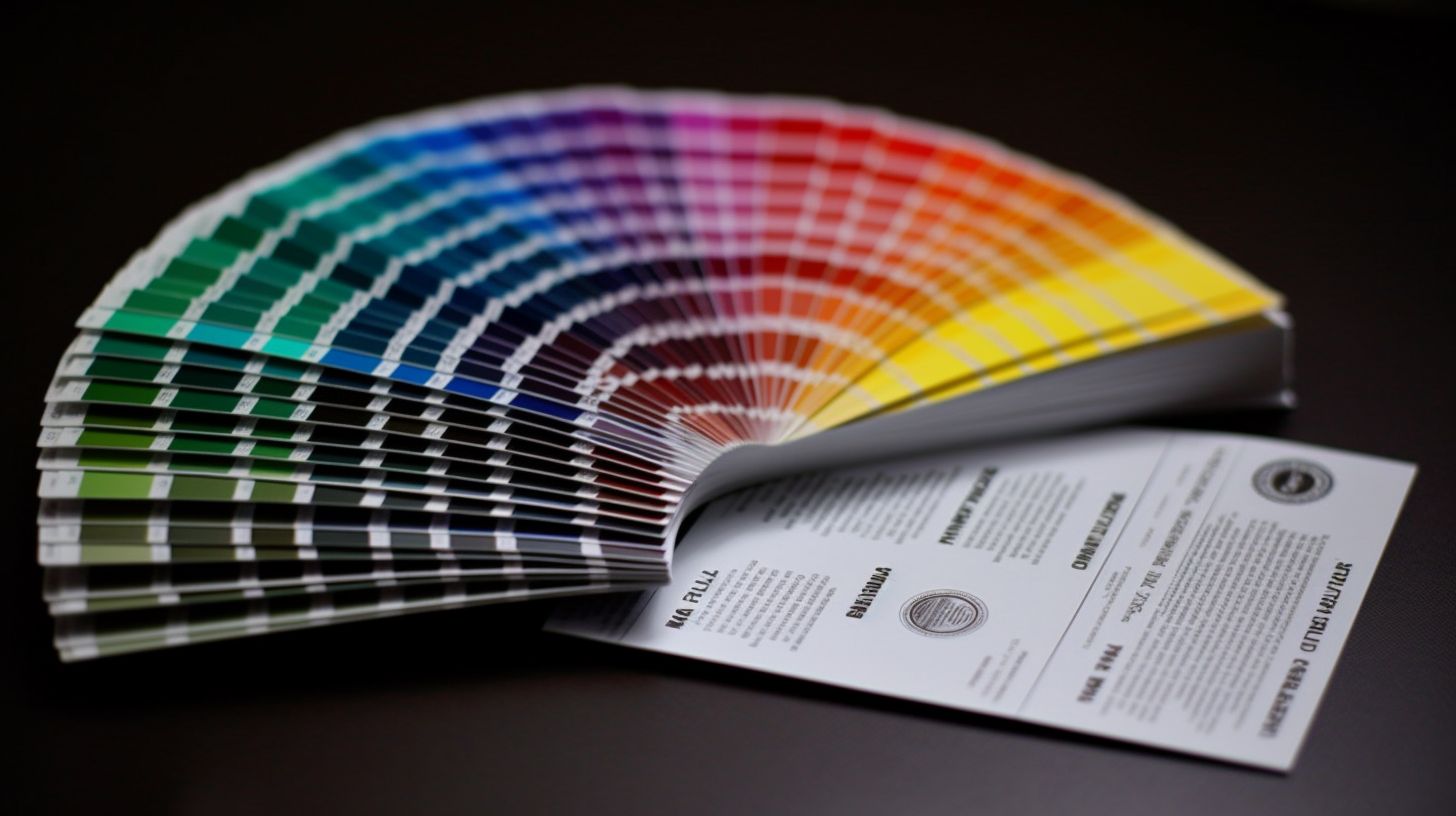
రంగు వ్యత్యాసాలను నియంత్రించడానికి మరియు ప్రింటింగ్లో రంగు ఖచ్చితత్వాన్ని సాధించడానికి, ప్రింటింగ్ ప్రక్రియలో ఆరు కీలక అంశాలను పరిగణనలోకి తీసుకోవడం చాలా ముఖ్యం.
కలర్ మిక్సింగ్: చాలా మంది ప్రింటింగ్ టెక్నీషియన్లు రంగులను సర్దుబాటు చేయడానికి అనుభవం లేదా వ్యక్తిగత తీర్పుపై ఆధారపడతారు, ఇది ఆత్మాశ్రయమైనది మరియు అస్థిరంగా ఉంటుంది. కలర్ మిక్సింగ్కు ప్రామాణిక మరియు ఏకీకృత విధానాన్ని ఏర్పాటు చేయడం ముఖ్యం. రంగు వ్యత్యాసాలను నివారించడానికి అదే తయారీదారు నుండి ప్రింటింగ్ ఇంక్లను ఉపయోగించడం సిఫార్సు చేయబడింది. కలర్ మిక్సింగ్ ముందు, ప్రింటింగ్ ఇంక్ యొక్క రంగును గుర్తింపు కార్డుకు వ్యతిరేకంగా తనిఖీ చేయాలి మరియు సరైన బరువు మరియు మీటరింగ్ పద్ధతులను ఉపయోగించి ఖచ్చితంగా కొలవాలి. రంగు మిక్సింగ్ ప్రక్రియలో డేటా యొక్క ఖచ్చితత్వం స్థిరమైన రంగు పునరుత్పత్తిని సాధించడానికి కీలకం.
ప్రింటింగ్ స్క్రాపర్: ప్రింటింగ్ ఇంక్ మరియు రంగు పునరుత్పత్తి యొక్క సాధారణ బదిలీకి ప్రింటింగ్ స్క్రాపర్ యొక్క కోణం మరియు స్థానం యొక్క సరైన సర్దుబాటు ముఖ్యం. ఇంక్ స్క్రాపర్ యొక్క కోణం సాధారణంగా 50 మరియు 60 డిగ్రీల మధ్య ఉండాలి మరియు ఎడమ, మధ్య మరియు కుడి సిరా పొరలను సుష్టంగా స్క్రాప్ చేయాలి. ప్రింటింగ్ సమయంలో రంగు స్థిరత్వాన్ని నిర్వహించడానికి స్క్రాపింగ్ కత్తి శుభ్రంగా మరియు సమతుల్యంగా ఉండేలా చూసుకోవడం కూడా చాలా ముఖ్యం.
స్నిగ్ధత సర్దుబాటు: ప్రింటింగ్ ఇంక్ యొక్క స్నిగ్ధత ఉత్పత్తి ప్రక్రియకు ముందు జాగ్రత్తగా నియంత్రించబడాలి. ఉత్పత్తి ప్రక్రియను ప్రారంభించడానికి ముందు ఊహించిన ఉత్పత్తి వేగం ఆధారంగా స్నిగ్ధతను సర్దుబాటు చేయడానికి మరియు ద్రావకాలతో సిరాను పూర్తిగా కలపాలని సిఫార్సు చేయబడింది. ఉత్పత్తి సమయంలో రెగ్యులర్ స్నిగ్ధత పరీక్ష మరియు స్నిగ్ధత విలువల యొక్క ఖచ్చితమైన రికార్డింగ్ మొత్తం ఉత్పత్తి ప్రక్రియను సర్దుబాటు చేయడంలో మరియు స్నిగ్ధతలో మార్పుల వల్ల కలిగే రంగు విచలనాలను తగ్గించడంలో సహాయపడుతుంది. శుభ్రమైన స్నిగ్ధత కప్పులను ఉపయోగించడం మరియు నాణ్యతను నిర్ధారించడానికి సాధారణ నమూనా తనిఖీలను నిర్వహించడం వంటి సరైన స్నిగ్ధత పరీక్ష పద్ధతులను ఉపయోగించడం చాలా ముఖ్యం.
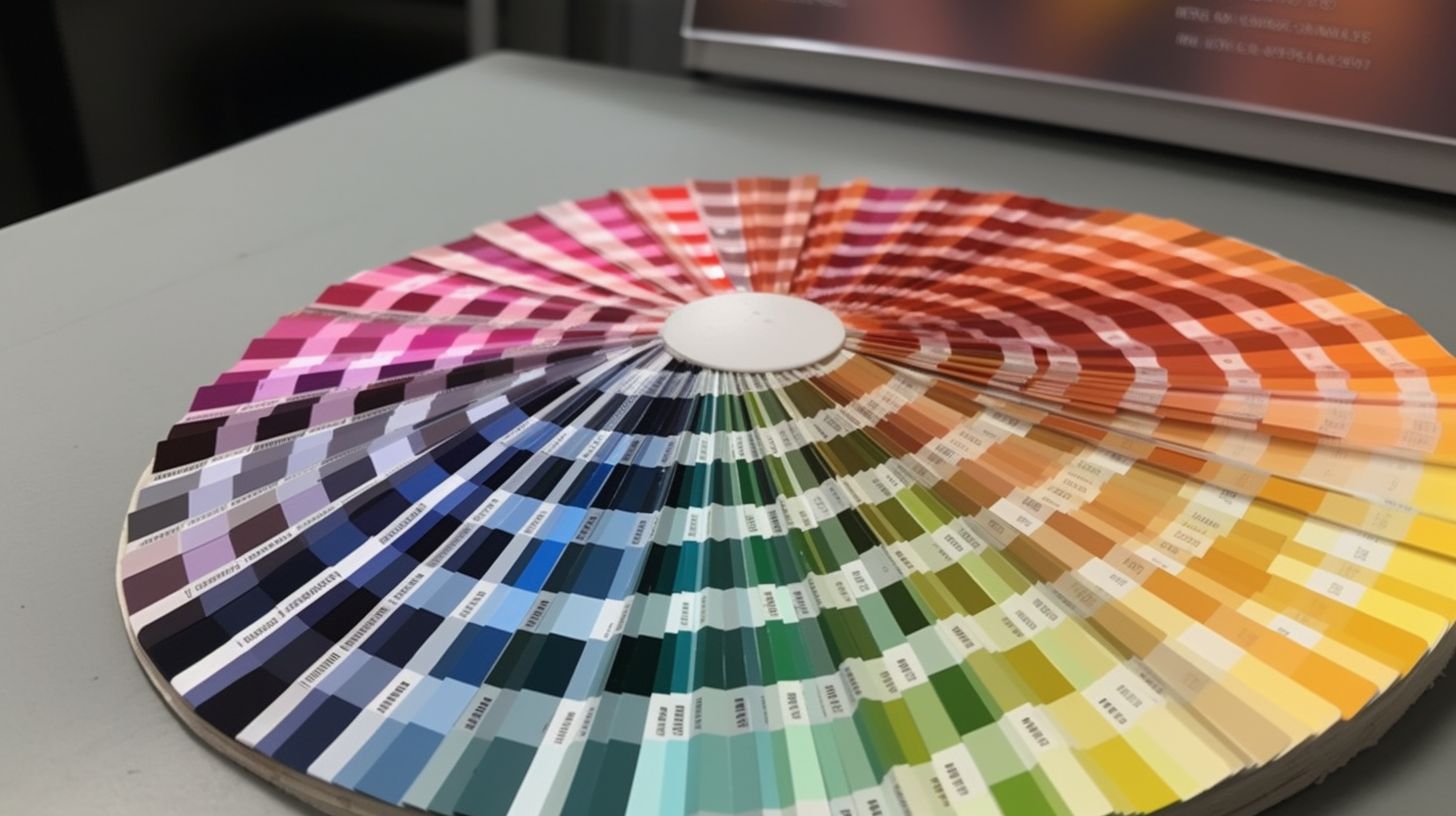
ఉత్పత్తి పర్యావరణం: వర్క్షాప్లోని గాలి తేమను తగిన స్థాయికి నియంత్రించాలి, సాధారణంగా 55% నుండి 65% మధ్య ఉండాలి. అధిక తేమ ప్రింటింగ్ ఇంక్ యొక్క ద్రావణీయతను ప్రభావితం చేస్తుంది, ముఖ్యంగా నిస్సార స్క్రీన్ ప్రాంతాలలో, పేలవమైన సిరా బదిలీ మరియు రంగు పునరుత్పత్తికి దారితీస్తుంది. ఉత్పత్తి వాతావరణంలో సరైన తేమ స్థాయిని నిర్వహించడం వలన ఇంక్ ప్రింటింగ్ ప్రభావాలను మెరుగుపరచవచ్చు మరియు రంగు వ్యత్యాసాలను తగ్గించవచ్చు.
ముడి పదార్థాలు: ప్రింటింగ్ ప్రక్రియలో ఉపయోగించే ముడి పదార్థాల ఉపరితల ఉద్రిక్తత రంగు ఖచ్చితత్వాన్ని కూడా ప్రభావితం చేస్తుంది. సరైన సిరా సంశ్లేషణ మరియు రంగు పునరుత్పత్తిని నిర్ధారించడానికి అర్హత కలిగిన ఉపరితల ఉద్రిక్తతతో ముడి పదార్థాలను ఉపయోగించడం ముఖ్యం. నాణ్యతా ప్రమాణాలను నిర్వహించడానికి ఉపరితల ఉద్రిక్తత కోసం ముడి పదార్థాలను క్రమం తప్పకుండా పరీక్షించడం మరియు తనిఖీ చేయడం నిర్వహించాలి.
ప్రామాణిక కాంతి మూలం: రంగులను తనిఖీ చేస్తున్నప్పుడు, రంగు వీక్షణ లేదా పోలిక కోసం అదే ప్రామాణిక కాంతి మూలాన్ని ఉపయోగించడం ముఖ్యం. విభిన్న కాంతి వనరుల క్రింద రంగులు విభిన్నంగా కనిపించవచ్చు మరియు ప్రామాణిక కాంతి మూలాన్ని ఉపయోగించడం స్థిరమైన రంగు మూల్యాంకనాన్ని నిర్ధారించడంలో మరియు రంగు వ్యత్యాసాలను తగ్గించడంలో సహాయపడుతుంది.
ముగింపులో, ప్రింటింగ్లో ఖచ్చితమైన రంగు పునరుత్పత్తిని సాధించడానికి సరైన రంగు మిక్సింగ్ పద్ధతులు, ప్రింటింగ్ స్క్రాపర్ను జాగ్రత్తగా సర్దుబాటు చేయడం, స్నిగ్ధత నియంత్రణ, తగిన ఉత్పత్తి వాతావరణాన్ని నిర్వహించడం, అర్హత కలిగిన ముడి పదార్థాలను ఉపయోగించడం మరియు రంగు మూల్యాంకనం కోసం ప్రామాణిక కాంతి వనరులను ఉపయోగించడం వంటి వివిధ అంశాలకు శ్రద్ధ అవసరం. ఈ ఉత్తమ పద్ధతులను అమలు చేయడం ద్వారా, ప్రింటింగ్ కంపెనీలు తమ ప్రింటింగ్ ప్రక్రియలను ఆప్టిమైజ్ చేయగలవు మరియు క్రోమాటిక్ అబెర్రేషన్ను తగ్గించగలవు, ఫలితంగా డిజైన్ డ్రాఫ్ట్లకు దగ్గరగా సరిపోలే అధిక-నాణ్యత ముద్రిత ఉత్పత్తులు లభిస్తాయి.
పోస్ట్ సమయం: మే-05-2023